焦粉的自动化控制系统如何设计和优化
焦粉的自动化控制系统设计和优化是一个综合性的任务,涉及硬件、软件、控制策略、故障检测与诊断以及数据管理与分析等多个方面。以下是一些建议的设计和优化措施:
一、系统硬件设计与优化
传感器与执行器选择:
选择高精度、高稳定性的传感器,如温度传感器、压力传感器、流量传感器等,用于实时监测焦粉生产过程中的各项参数。
选用可靠的执行器,如电机、阀门等,用于控制焦粉的输送、混合、加热等过程。
控制器与通信设备:
采用性能稳定的控制器,如PLC(可编程逻辑控制器),实现对焦粉生产过程的自动化控制。
建立冗余配置的通信网络,如冗余工业以太网交换机,以提高系统的可靠性和容错性。
硬件升级与冗余配置:
对关键硬件设备进行更新换代,如采用性能更稳定的控制器、变频器等。
增加冗余配置,如冗余控制站,以提高系统的整体可靠性。
二、软件设计与优化
监控软件与数据分析:
开发监控软件,实现对焦粉生产过程的实时监控和数据分析。
利用大数据技术对生产数据进行分析和挖掘,发现生产过程中的问题和改进点。
控制程序优化:
对控制程序进行优化,减少不必要的计算和资源消耗,提高程序的执行效率。
引入先进的控制算法,如PID控制、模糊控制等,以提高控制精度和稳定性。
软件界面优化:
对控制系统的操作界面进行优化设计,使其更加简洁、直观、易用。
引入自动化和智能化技术,减少人工操作量,降低操作难度。
三、控制策略优化
自动化配煤控制:
引入自动化配煤系统,实现焦粉的精确配比和混合。
利用PLC控制系统实现配煤过程的自动化控制,提高配煤效率和精度。
温度与压力控制:
采用先进的温度与压力调节算法,实现对焦粉生产过程中的温度和压力的精确控制。
引入先进的传感器和执行器,提高温度与压力控制的稳定性和精度。
循环与排料控制:
设计合理的循环与排料控制策略,确保焦粉在生产线上的稳定流动和高效利用。
利用自动化控制系统实现循环与排料过程的自动化控制,减少人工干预和等待时间。
四、故障检测与诊断优化
建立故障预警系统:
通过实时监测关键设备的运行状态和参数,及时发现潜在的故障隐患。
引入故障预警算法,对潜在故障进行早期识别和预警。
提高故障诊断能力:
建立完善的故障诊断知识库和专家系统,以便在故障发生时能够迅速定位并给出解决方案。
引入人工智能和机器学习技术,提高故障诊断的准确性和效率。
五、数据管理与分析优化
建立基础数据库:
对工艺内各系统进行数据采集,建立基础数据库,为数据分析和系统建模提供数据支持。
实现数据可视化,通过数据可视化技术将生产数据、设备数据等实时展示给操作人员和管理人员。
数据挖掘与分析:
利用大数据技术对生产数据进行分析和挖掘,发现生产过程中的问题和改进点。
通过数据分析结果指导生产优化和决策制定,提高生产效率和产品质量。
综上所述,焦粉的自动化控制系统设计和优化需要从系统硬件、软件、控制策略、故障检测与诊断以及数据管理与分析等多个方面入手。通过合理的工艺设计和设备选型以及优化措施的实施,可以实现焦粉生产过程的高效、稳定、可控和智能化。
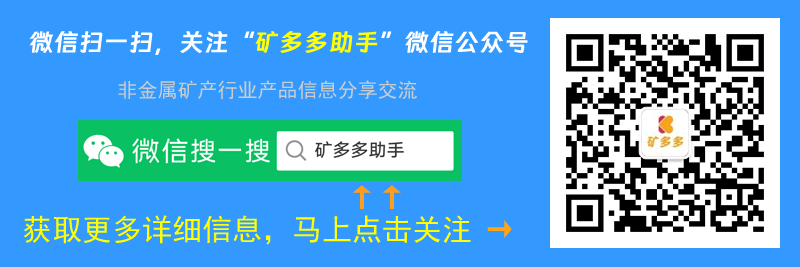
版权声明:本站所发布信息均整理自互联网具有公开性、共享性的信息,发布此信息旨在传播更多信息之目的,不代表本网站立场,转载请联系原作者并注明出处,如果侵犯了您的权益请与我们联系,我们将在24小时内更正、删除。