人工智能如何预测冶炼焦炭生产中的故障风险
人工智能(AI)在冶炼焦炭生产中的故障风险预测方面具有显著优势,通过机器学习、深度学习和大数据分析等技术,能够实时监测设备状态、分析生产数据,并提前预测潜在故障,从而优化生产流程、降低维护成本并提高生产效率。以下是AI在这一领域的主要应用和实现方式:
1.数据采集与实时监测
AI技术依赖于大量的生产数据,包括设备运行参数(如温度、压力、流量)、传感器数据、历史故障记录等。通过自动化生产线和智能监控系统,可以实时采集这些数据,并利用大数据技术进行处理和分析。
2.故障预测模型的构建
利用机器学习算法(如随机森林、支持向量机、神经网络)和深度学习模型(如卷积神经网络、循环神经网络),可以构建故障预测模型。这些模型能够识别设备故障的模式和趋势,提前预测潜在故障。
例如,湘钢通过AI技术实现了对高炉焦炭质量的预测,以及对设备故障的实时监测和预警,显著提升了生产效率和设备可靠性。
3.优化维护计划
AI不仅可以预测故障,还能优化维护计划。通过分析设备的历史数据和实时运行状态,AI系统可以确定最佳的维护时间点,减少不必要的维护工作,降低维护成本。
4.实际应用案例
临涣焦化:通过部署设备在线监测与故障诊断系统,AI技术已成功预测近300起故障隐患,避免了设备停机和安全事故,同时提升了设备的平均运行时间。
硕橙科技:利用声振机械特征值算法和机器学习技术,为钢铁冶金行业提供设备智能运维服务,故障识别准确率可达95.3%。
5.技术优势与效益
提高预测准确性:AI模型能够识别复杂的非线性关系,比传统统计方法更准确地预测故障。
降低维护成本:通过提前预测故障,企业可以安排计划性维护,减少突发故障带来的经济损失。
提升生产效率:AI技术可以优化生产参数,提高焦炭质量,减少生产过程中的波动。
6.未来发展方向
多模型融合:结合多种机器学习和深度学习模型,进一步提高故障预测的准确性和可靠性。
数字化双胞胎技术:通过构建虚拟生产模型,模拟不同工况下的设备运行状态,优化生产流程。
智能化运维平台:开发集成AI技术的运维平台,实现设备全生命周期管理。
综上所述,人工智能在冶炼焦炭生产中的故障风险预测方面已经取得了显著进展,通过实时数据采集、智能模型构建和优化维护计划,能够有效降低生产风险、提高设备可靠性和生产效率。
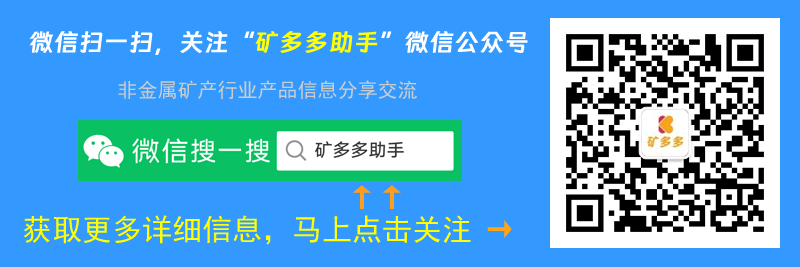
版权声明:本站所发布信息均整理自互联网具有公开性、共享性的信息,发布此信息旨在传播更多信息之目的,不代表本网站立场,转载请联系原作者并注明出处,如果侵犯了您的权益请与我们联系,我们将在24小时内更正、删除。