焦炉煤气在冶炼焦生产中有哪些回收利用方式
焦炉煤气在冶炼焦生产中有着多种回收利用方式,这些方式不仅有助于资源的有效利用,还能减少环境污染。以下是一些主要的回收利用途径:
一、作为加热燃料
焦炉煤气可以作为不同加热设备的气体燃料,与固体燃料相比,它具有使用便捷、可以管道输送和传热效率高等优点。在工业上,它可以用于焦炉加热、轧钢加热炉、高炉热风炉、烧结点火等。然而,随着企业内能量利用率的提高和替代燃料(如高炉煤气)的使用,加热所需要的焦炉煤气量正在逐渐减少。在民用方面,经过净化的焦炉煤气也可以作为燃气供当地居民使用,但近年来随着天然气等清洁能源的普及,其作为民用燃料的需求量也在下降。
二、发电
将焦炉煤气用于发电是近年来主要的利用途径之一。我国焦炉煤气发电一般有三种方式:蒸气发电、燃气轮机发电和内燃机发电。
蒸气发电:通过燃烧焦炉煤气产生蒸汽,进而驱动蒸汽轮机发电。
燃气轮机发电:直接燃烧焦炉煤气来驱动燃气轮机带动发电机组发电,具有燃机运行效率高、设备占地少、建设工期短、回收周期短、效益良好的特点。但燃气轮机对焦炉煤气的要求较高,必须经过严格净化,并且对焦炉煤气的热值要求也很高。同时,燃机余热还会带走大量热能,造成损失。此外,燃气轮机还面临着可靠性差和使用寿命短的问题。
内燃机发电:由火花塞点火,运用煤气机带动发电机组发电,发电效率相对较高,可达30%~40%。这种方法是热能直接转化成机械能,能量的转化率高,运行效率高,辅助设备少,投入少回报快,适合中型焦化厂使用。
对于独立焦化厂而言,在利用焦炉煤气发电时,多采用的是燃气内燃机技术,其设备投资较小且焦炉煤气成本低,所以经济效益显著。而对于国内大中型钢铁企业而言,在利用焦炉煤气发电时,多采用的是燃气-蒸气联合循环发电技术(CCPP),但普遍存在设备一次性投资大、维护及备件费用高、电价居高不下等问题。
三、生产纯氢
焦炉煤气中氢气资源相当丰富,氢气的体积百分含量超过50%。利用焦炉煤气生产纯氢的主要方法有深冷法和变压吸附法(PSA法)。
深冷法:利用焦炉气中各主要成分冷凝温度的不同,以深度冷冻部分冷凝的方法使氢与其它气体组分分离,最后用液氮洗以脱除气体中剩余的CO和CH4。最终得到的气体中氢气含量可达83%~88%,其余为氮。但深冷法所用设备复杂且需在高压下操作,这使得深冷装置投资大、运转费用高、投资回收期长,因此难以被大多数焦化厂接受。
变压吸附法(PSA法):利用气体组分在固体材料上吸附特性的差异以及吸附量随压力变化而变化的特性,通过周期性的压力变换过程实现气体的分离或提纯。在我国已有多年的历史,其生产技术成熟,经济合理。但与水电解法制氢相比,焦炉煤气生产纯氢需要具备管道输送的固定用户,一旦用户发生变化,很难维持正常生产,只能转产。
四、合成甲醇
焦炉煤气组分中甲烷含量(体积分数)为24%~28%,只需将甲烷转化成一定比例的CO和H2,即可满足合成甲醇的合成气比例要求。合成甲醇的主要反应为:CO+2H2=CH3OH+Q和CO2+3H2=CH3OH+H2O+Q。煤气中甲烷及高碳烃转化成合成气后,在60MPa压强下即可完成甲醇合成,流程短,反应速度快,焦炉煤气利用率高。一般2000~2200m³焦炉煤气可生产1t甲醇。但对于钢铁企业而言,要利用焦炉煤气合成甲醇主要存在两方面问题:一是需要有充足的焦炉煤气富余量,生产1t甲醇需消耗2000~2200m³的焦炉煤气;二是投资规模较大。
五、生产直接还原铁(DRI)
理论上讲,焦炉煤气不需要经过热裂解,就可直接供给气基竖炉生产海绵铁。其工艺过程为:将焦炉煤气和竖炉顶气混合而成的还原气在加热炉中加热,然后直接通入到直接还原炉中生产直接还原铁。在此过程中,焦炉煤气作为还原过程的还原气,而高炉煤气则作为燃料用于加热还原气体。然而,利用焦炉煤气生产直接还原铁虽然技术上可行,但距离规模化、产业化应用还有一定的距离。主要原因在于焦炉煤气资源问题:对于钢铁企业内部的焦化厂而言,焦炉煤气主要用于钢铁厂内热能平衡,其富余的焦炉煤气量不足以供应DRI的生产需求;而对于独立焦化企业而言,焦炉煤气约40%~50%用于加热焦炉,其剩余气量也很难满足DRI生产的需要。
综上所述,焦炉煤气在冶炼焦生产中有着多种回收利用方式。这些方式不仅有助于资源的有效利用和减少环境污染,还能提高企业的经济效益和社会效益。
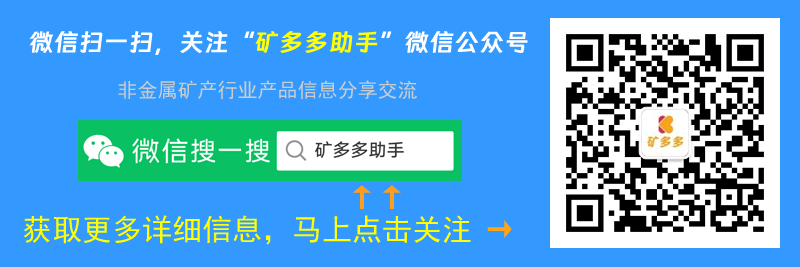
版权声明:本站所发布信息均整理自互联网具有公开性、共享性的信息,发布此信息旨在传播更多信息之目的,不代表本网站立场,转载请联系原作者并注明出处,如果侵犯了您的权益请与我们联系,我们将在24小时内更正、删除。